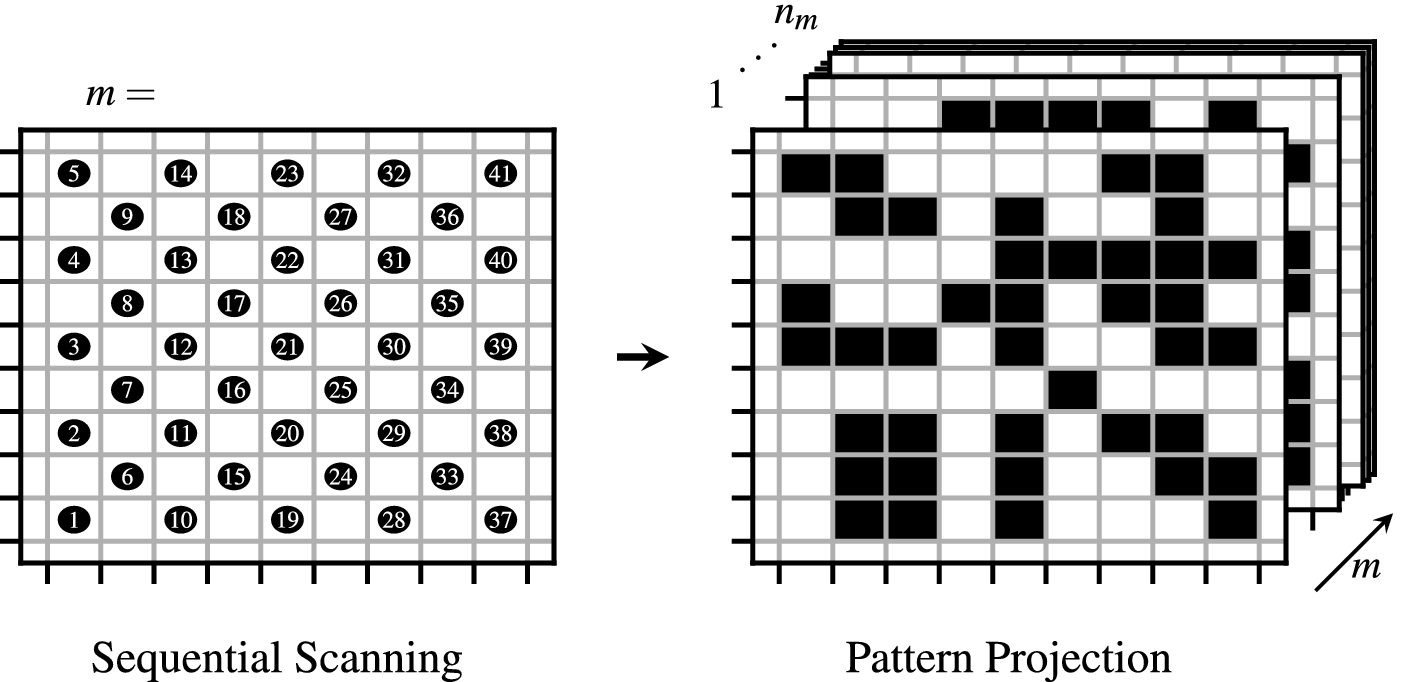
Real-time Defect Detection in Metal 3D Printed Parts
Additive manufacturing has revolutionized the way manufacturing is done, and it is an industry that continues to grow rapidly. One of the most significant advantages of 3D printing is its ability to create complex shapes and geometries that were not possible with traditional manufacturing techniques. However, the quality of parts produced through 3D printing is not always consistent, and defects can occur. Identifying and correcting defects early in the manufacturing process is essential to ensure high-quality parts. This is where real-time defect detection comes in. In this article, we will discuss how researchers at Lawrence Livermore National Laboratory (LLNL) have developed a method for real-time defect detection in metal 3D printed parts.
The Need for Real-Time Defect Detection in 3D Printing
3D printing, or additive manufacturing, involves building objects layer by layer using computer-aided design (CAD) models. Unlike traditional manufacturing techniques, 3D printing allows for the creation of complex geometries and shapes. The process of 3D printing can involve several steps, including material preparation, printing, post-processing, and quality assurance.
Also Read:
Defects can occur at any stage of the 3D printing process, and identifying them early is critical to ensure high-quality parts. Defects can take many forms, such as porosity, cracks, and inclusions, and can lead to part failure. Traditional methods of defect detection involve post-processing and inspection, which can be time-consuming and costly. Real-time defect detection during the printing process can enable early detection and correction of defects, leading to higher-quality parts and reduced costs.
The LLNL Method for Real-Time Defect Detection
Researchers at LLNL have developed a method for real-time defect detection in metal 3D printed parts. The method involves using a high-speed camera to capture images of the printing process, and then using computer vision algorithms to analyze the images in real-time. The algorithms can detect defects such as pores, cracks, and inclusions as they occur during the printing process.
The LLNL researchers tested their method on several metal alloys, including titanium, aluminum, and stainless steel. The results showed that the method was able to detect defects in real-time, with a high degree of accuracy. The method was also able to detect defects that were not visible to the naked eye.
The Benefits of Real-Time Defect Detection
Real-time defect detection in 3D printing offers several benefits. Early detection of defects can lead to higher-quality parts and reduced costs. Defects can be corrected before the printing process is complete, reducing the need for post-processing and inspection. Real-time defect detection can also help identify the root causes of defects, leading to process improvements and better quality control.
Real-time defect detection can also help accelerate the adoption of 3D printing in industries such as aerospace, automotive, and medical. These industries have strict quality requirements, and the ability to produce high-quality parts consistently is essential. Real-time defect detection can help ensure that 3D printing meets these requirements.
Conclusion
In conclusion, real-time defect detection is a critical component of the 3D printing process. Researchers at LLNL have developed a method for real-time defect detection in metal 3D printed parts using high-speed cameras and computer vision algorithms. The method offers several benefits, including higher-quality parts, reduced costs, and process improvements. Real-time defect detection can help accelerate the adoption of 3D printing in industries that require strict quality control. As additive manufacturing continues to grow, real-time defect detection will become increasingly important.
Keywords: 3D printing, additive manufacturing, defect detection, real-time, high-speed cameras, computer vision, quality control.
Read More:
That's it for this article.
Thanks for Visiting Us – fixyanet.com
0 Comments